Environmental Statement
Environmental Statement
Our Investment For The Future
It is Keymark’s policy and responsibility to be environmentally friendly to the communities where we manufacture as well as the areas in which our extrusions are installed and maintained. We are continually focused on improving our aluminum extrusion manufacturing operations to reduce waste and maximize efficiency. The following are areas in which we demonstrate our dedication and efforts to eliminate those wastes, control pollution, and focus on recycling/recovery.
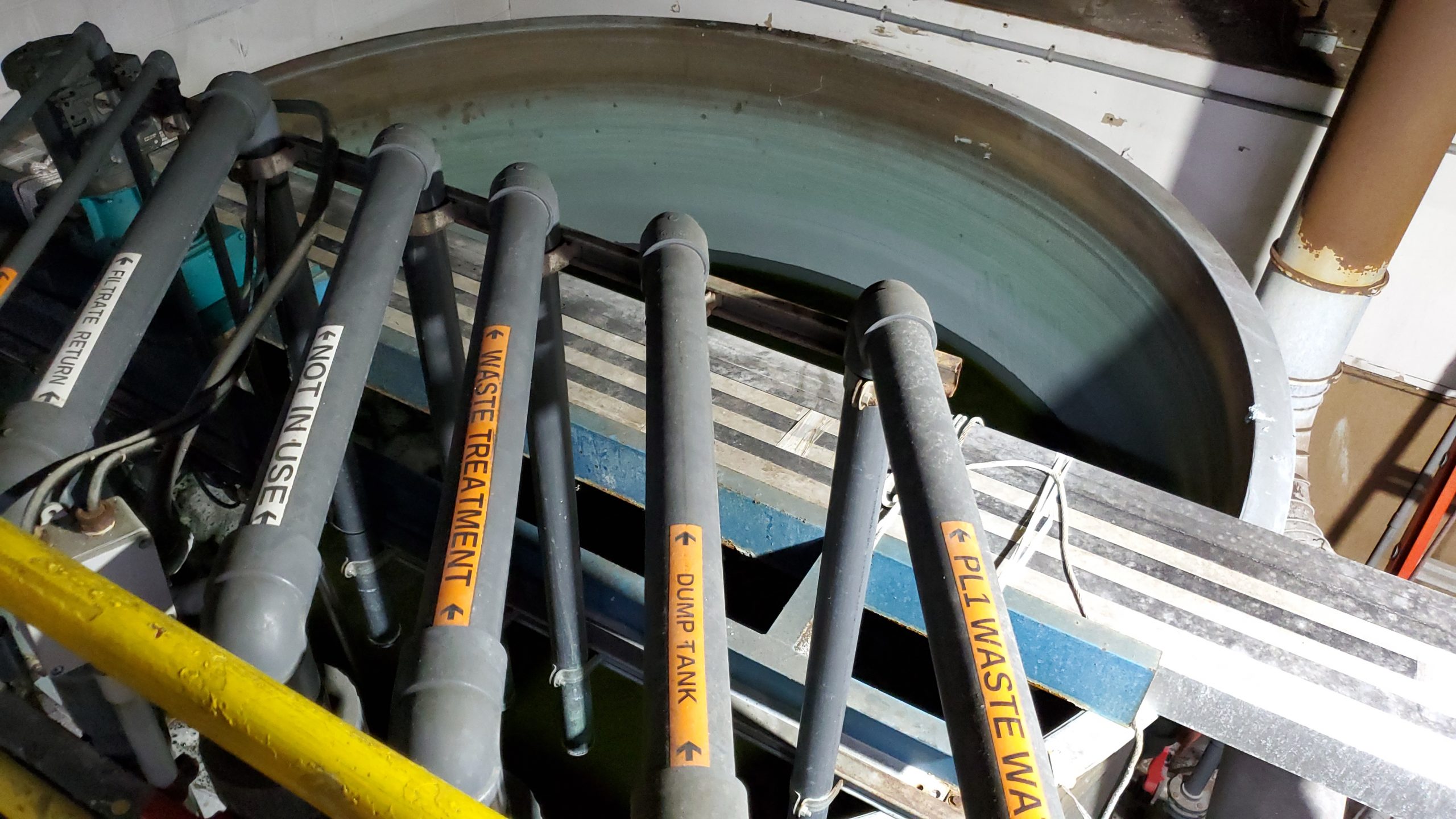
Casting
Keymark Corporation extrudes over eighty-percent of its weekly production lbs. from prime aluminum billet produced internally at our secondary casting facility. Over 38% of the aluminum billet is composed from recycled internal or outside purchased aluminum scrap. Documentation may be provided to help ensure the requirements of the U.S. Green Building Council.
Dross, which is a waste by-product of the casting process (40,000/lbs. weekly), is sent to an aluminum smelter for continuous recycled use.
Due to the recent upgrade to the regenerative burners in the melting unit, this upgrade resulted in a reduction of 171.8 million cubic feet annually of natural gas savings. Also as a result of this upgrade, Keymark reduced 2.83 tons of carbon monoxide emissions annually.
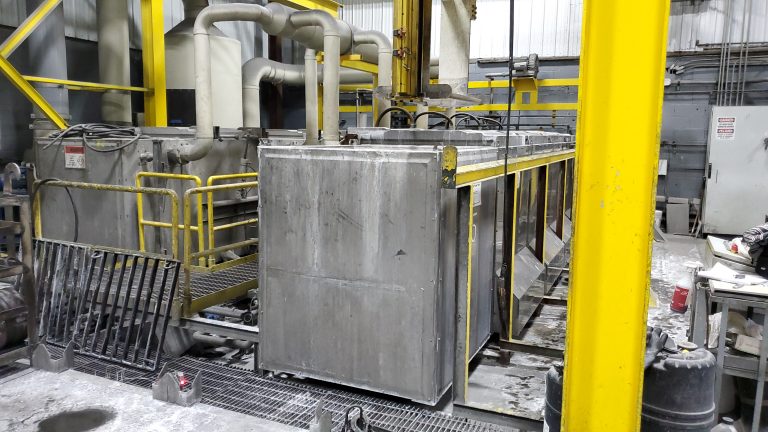
Extrusion (Die Shop)
Caustic (Sodium Hydroxide) Scrubber Unit – Removes the caustic out of the air before exhausting to the atmosphere.
Paint Lines
Acetone and Xylene are used to clean the paint equipment and flush out the lines between color changes. They are 100% recycled on site and recovered for reuse.
Thermal Oxidizers – Keymark runs 3 thermal oxidizers on our paint lines. The 3 units have a destruction efficiency of 96% of the volatile organic compounds (VOC’s) removal rate prior to emission to the atmosphere. This destruction efficiency rate eliminates 799,677 lbs. annually of VOC emissions.
Waste Water Treatment – The painting process creates over 7.1 million gallons of anodizing waste water annually. The waste water goes through our full in-house water treatment system and we meet or exceed all (NYSDEC) New York State Dept. of Environmental Conservation and (USEPA) United States Environmental Protection Agency regulations prior to the water being discharged.
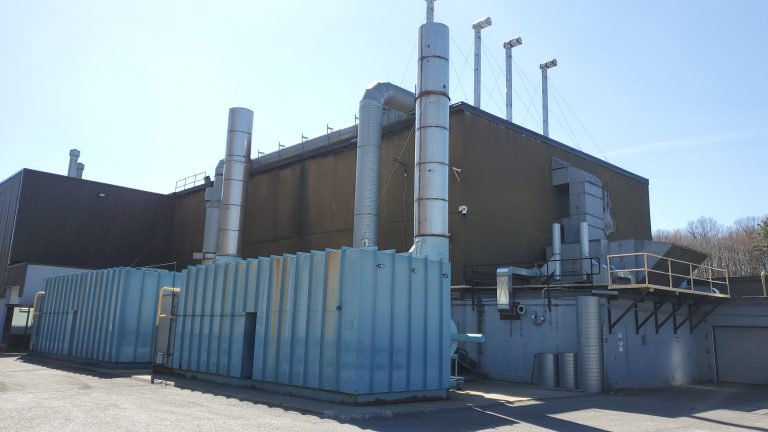
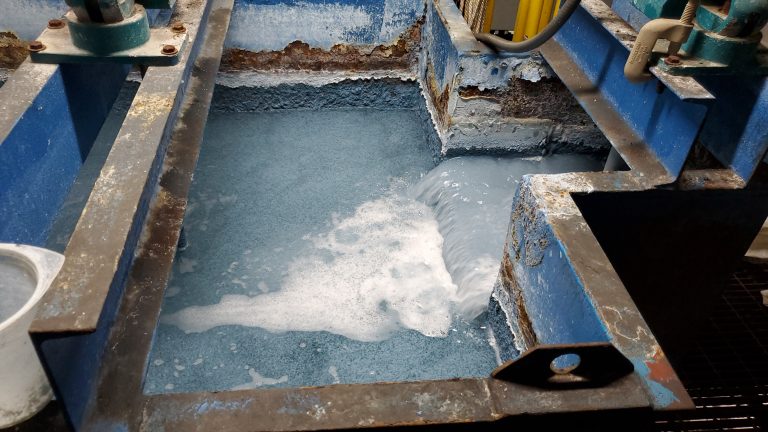
Anodizing
The anodizing process utilizes 2 chemical recovery units:
Caustic Recovery Unit – Removes dissolved aluminum from the caustic, thus allowing the caustic to be continuously re-used. This process eliminates 228 annual tons of waste (Aluminum Trihydrate) that would otherwise find it’s way to a local landfill. This material is given to an industry that uses it as a beneficial re-use product in their manufacturing process.
APU (Acid Purification Unit) – In the anodizing process, the APU removes excess aluminum from the solution and the solution is then returned back to the anodizing tanks for continuous re-use. This recovery prevents the need for treatment or wasting the used solution.
Waste Water Treatment – The anodizing process creates over 42 million gallons of anodizing waste water annually. The waste water goes through our full in-house water treatment system and we meet or exceed all (NYSDEC) New York State Dept. of Environmental Conservation and (USEPA) United States Environmental Protection Agency regulations prior to the water being discharged.
Thermal Break
In the thermal break department, left over aluminum chips combined with polyurethane are inherent in the process, due to the debridging operation. The aluminum/polyurethane chips are not recycled internally, due to the toxicity of emissions if Keymark were to utilize our melting facility internally, instead the material is sent to a recycler for separation and re-use.
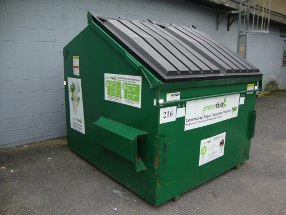
Packaging
All of our cardboard used in the packaging process is of 100% recycled content. Also, all of our leftover cardboard or scrap is then turned back over to a recycler.